For my first Formula project, I designed a custom steering wheel and dashboard to enhance driver ergonomics and visibility. My steering wheel design featured a modular grip system—3D-printed in two halves that bolt onto the wheel—solving two key issues: driver comfort and adjustability. This allowed for a more comfortable grip while also enabling the steering wheel to expand for larger drivers. The dashboard was optimized for maximum visibility, ensuring crucial data could be read quickly during races.
My experience in design includes the floor close out, critical fasteners, tabs, welding jigs, and ergonomics jigs. For floor close out, I used carbon fiber with aluminum honey comb to balance strength and weight efficiency. I ensured for all the critical fasteners I designed met tear-out strength calculations requirements according to FSAE standards. For non critical fasteners, I designed numerous tabs to support non-structural components efficiently. Welding jigs were needed to weld all the parts I designed onto the car. To accomplish this, I developed a system of 3d printed and wood parts to support and hold all fasteners in there correct positioning while being welded. I designed and built an ergonomics jig designed to real life test the positioning of the steering column, brakes, seat and headrest angle.
My manufacturing experience includes CNC machining, 3D printing, and composite layups and infusions. I also assisted in fabricating the floor close-out, utilizing carbon fiber and aluminum honeycomb panels for an optimized strength-to-weight ratio. My duties also included fastener installation and welding jig setup, ensuring proper alignment and structural integrity during assembly. Throughout the process, I collaborated closely with machinists and welders, iterating upon designs to improve manufacturability and ease of production.
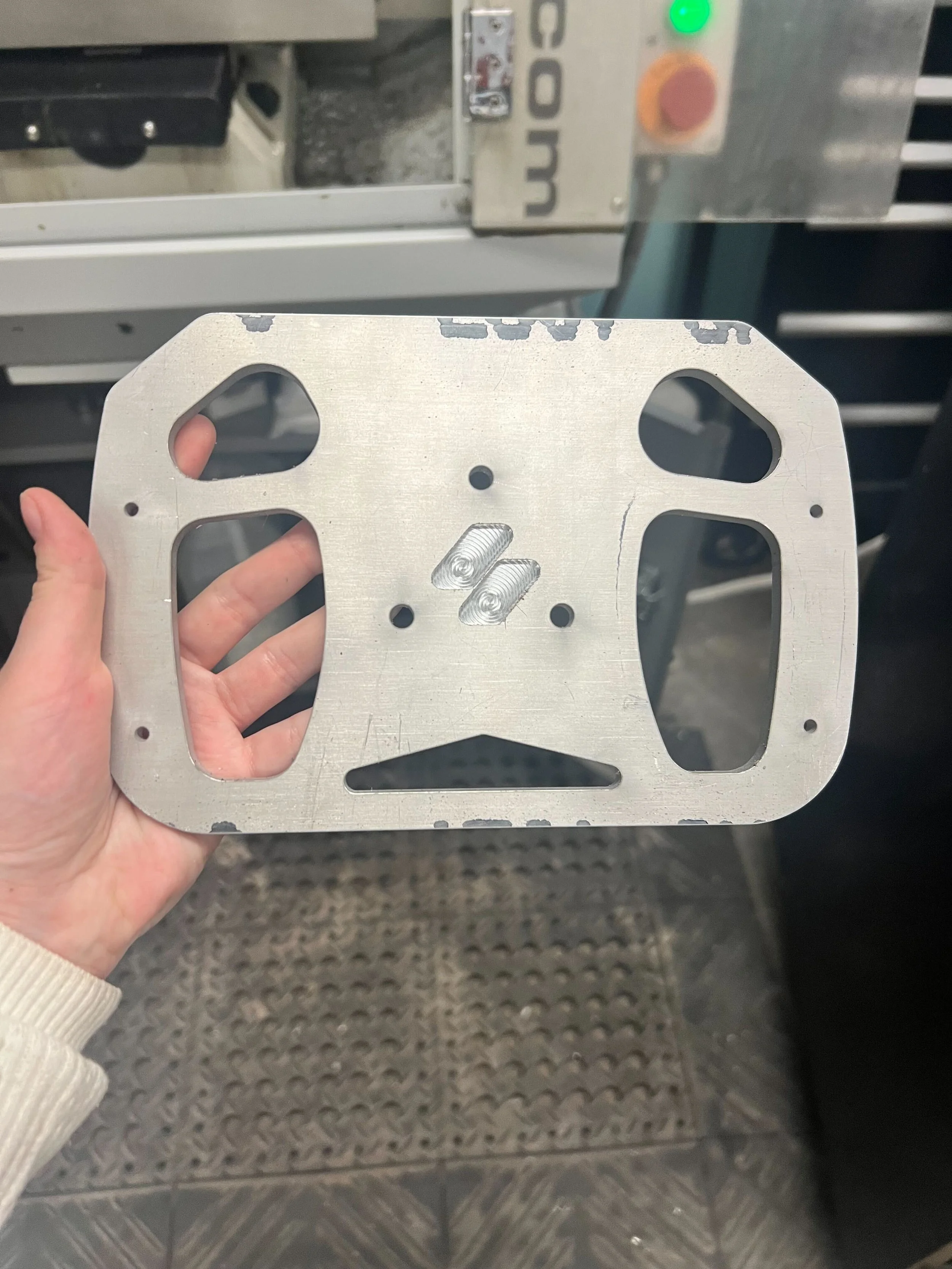
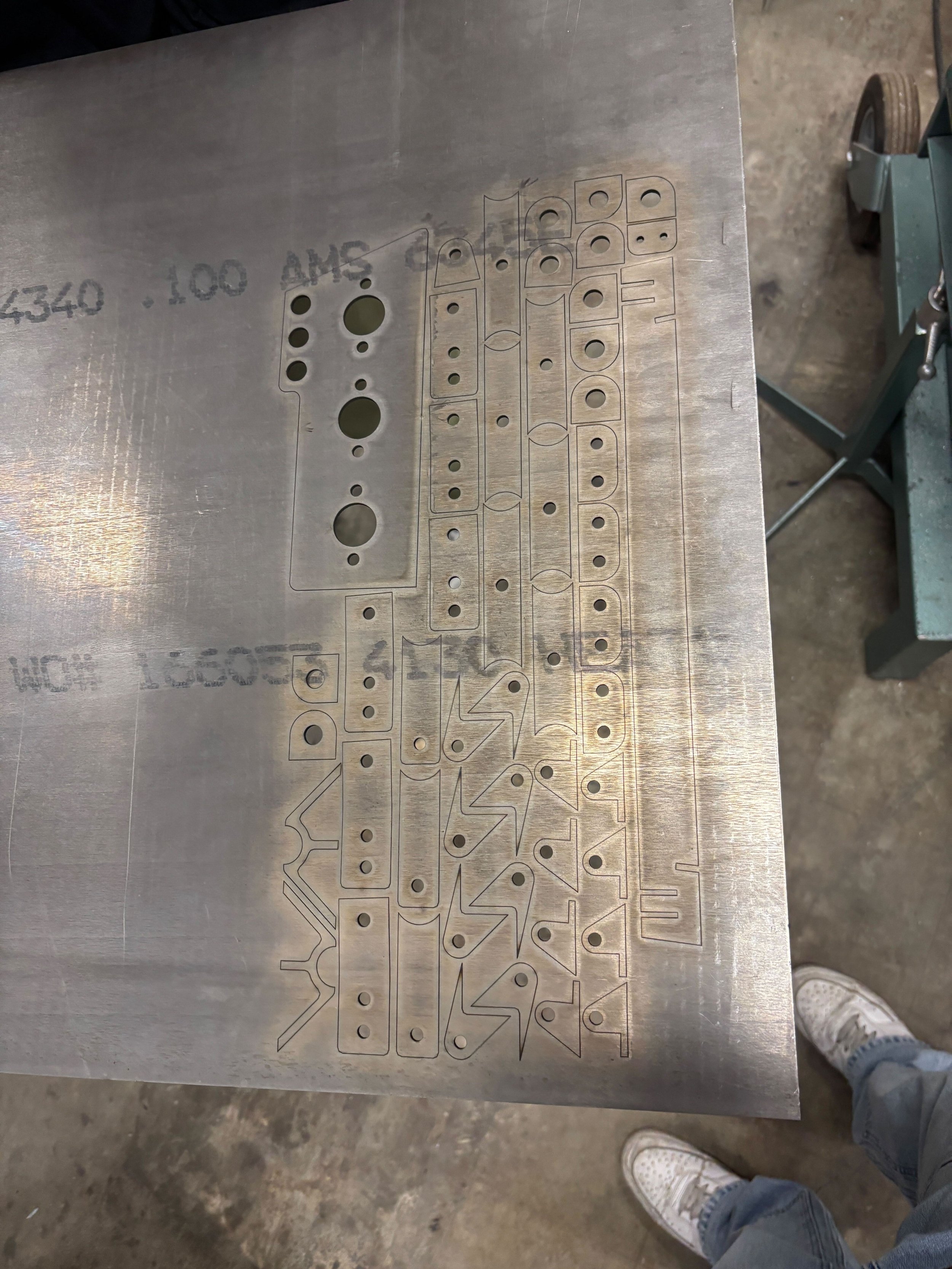
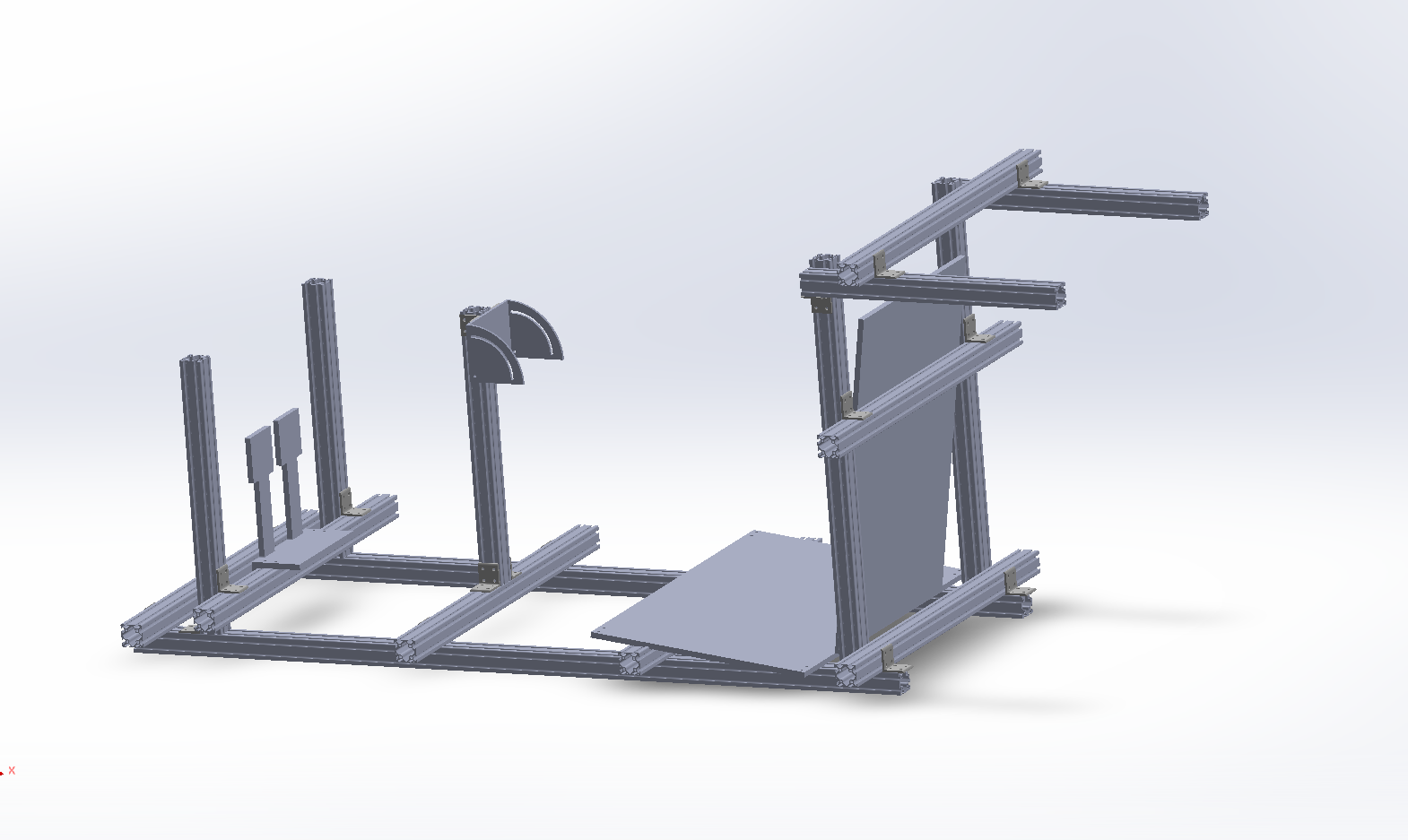
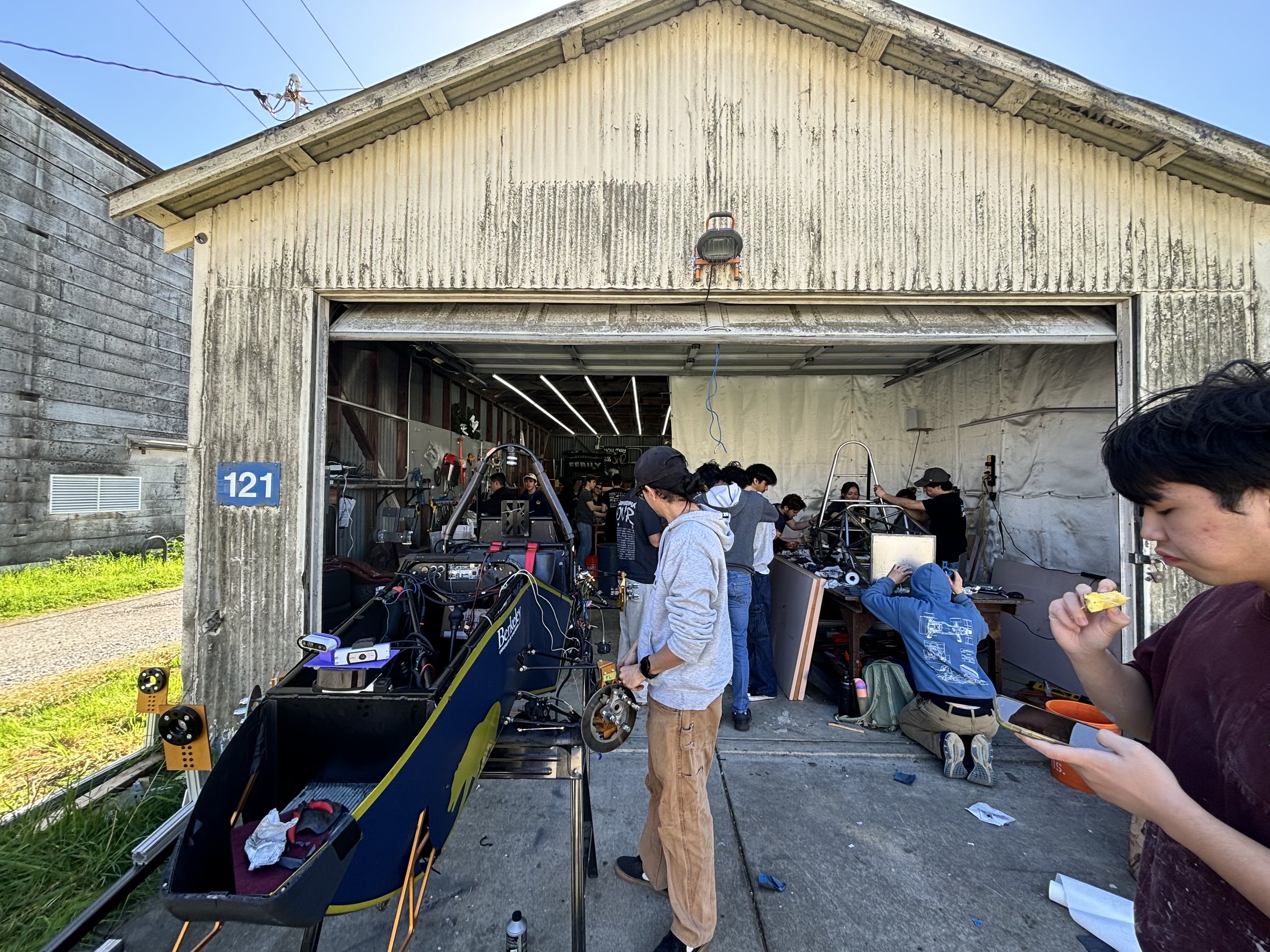
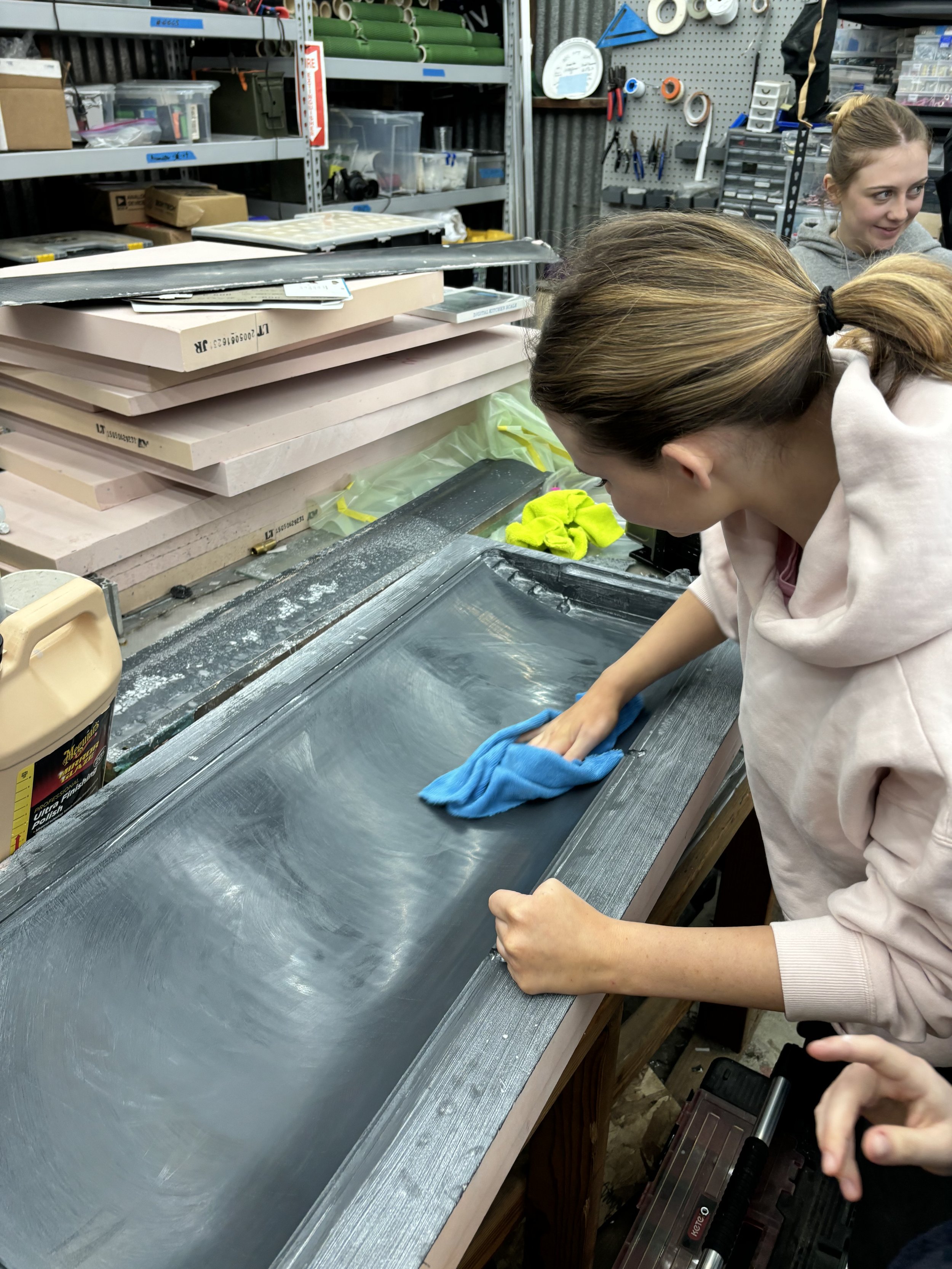

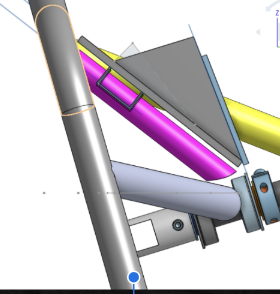

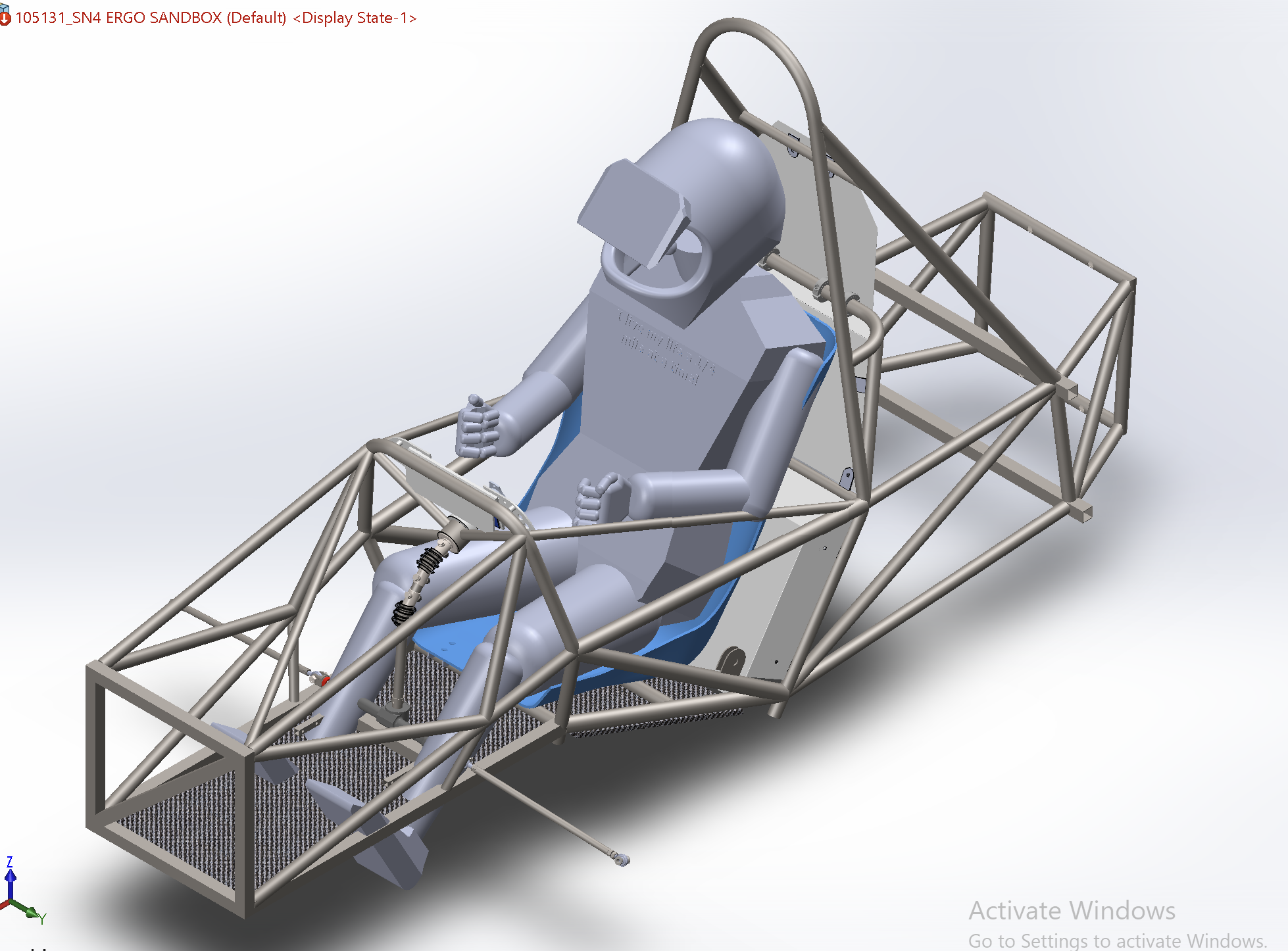


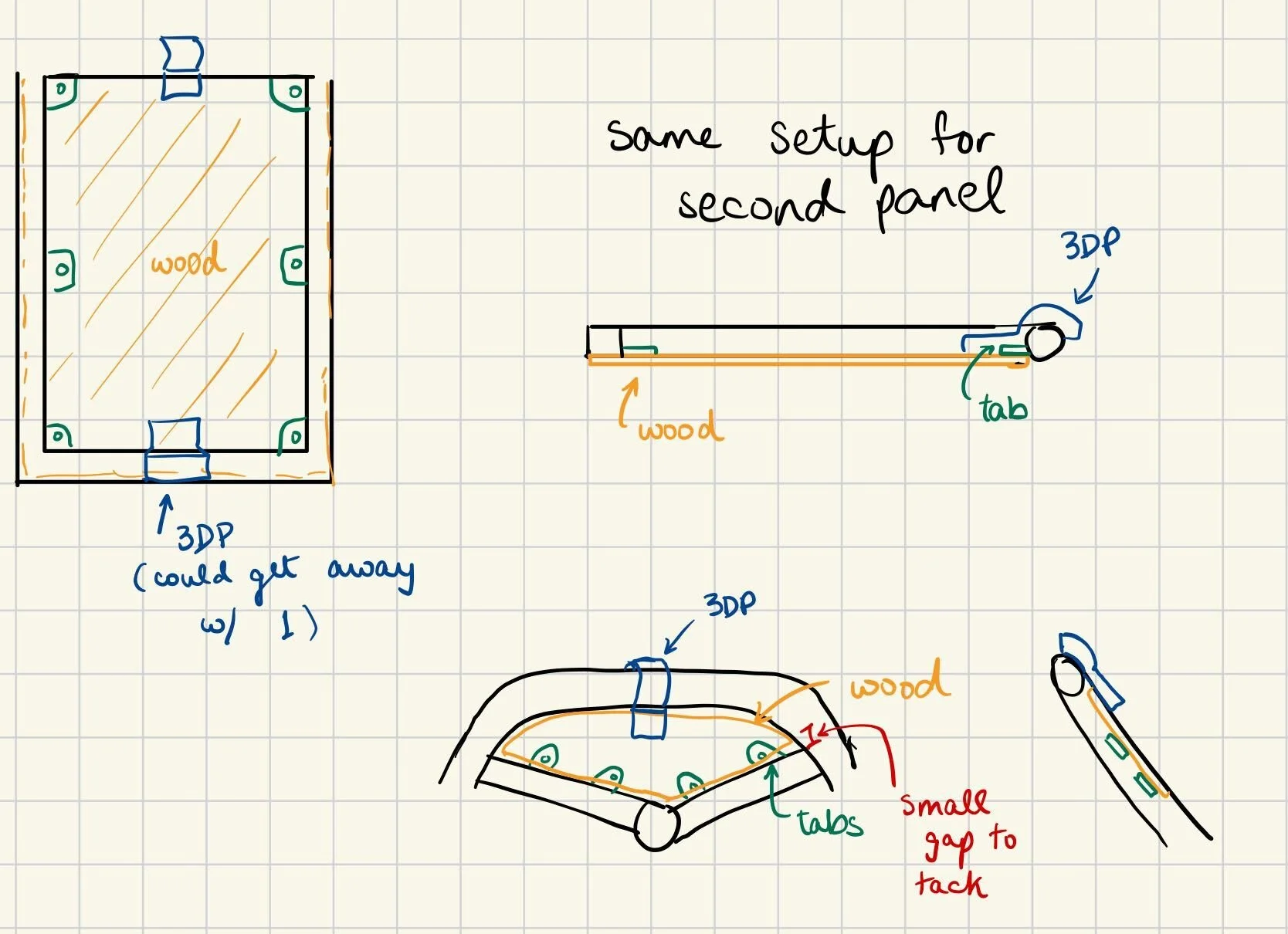
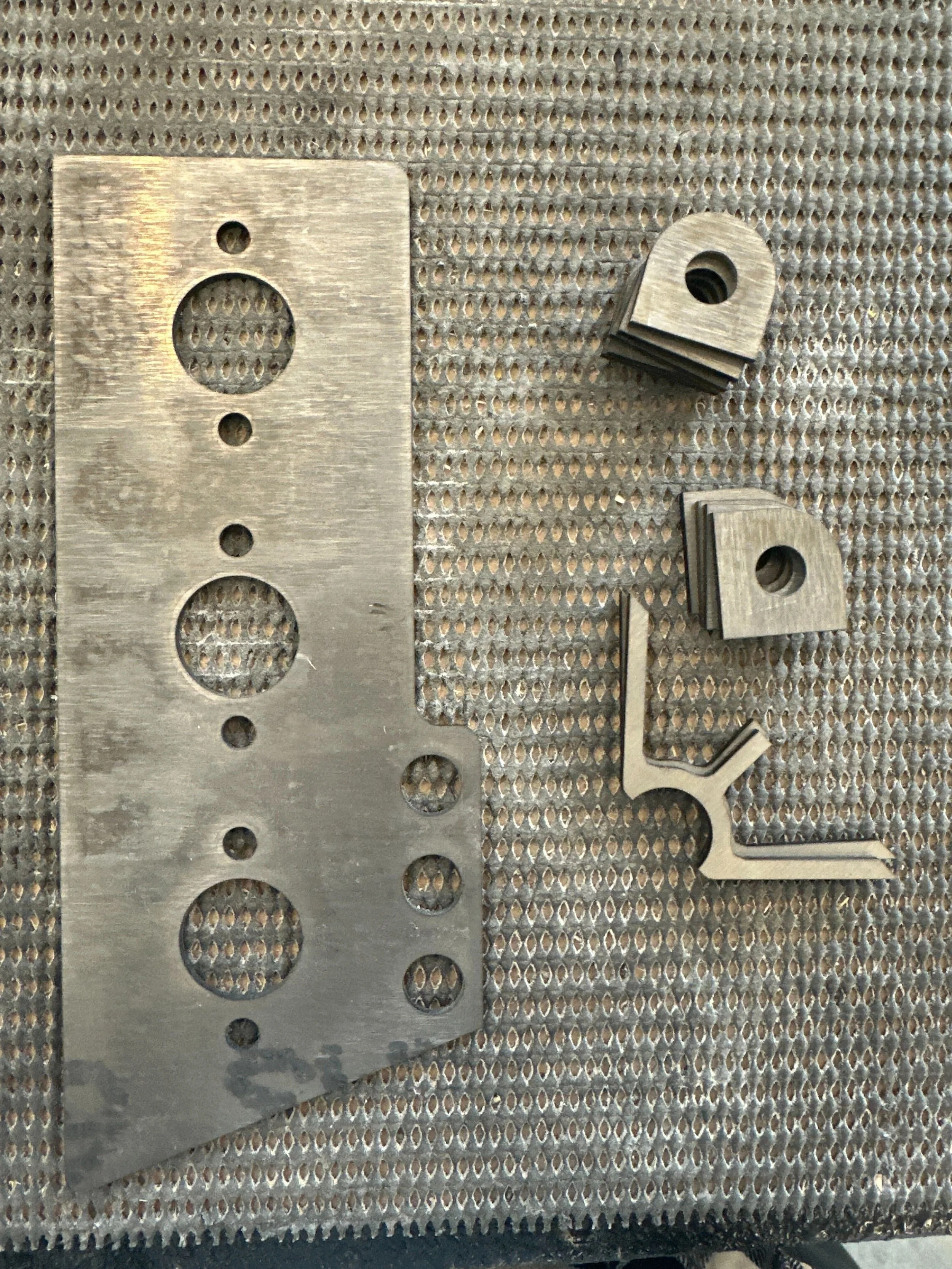
Time Lapse of a carbon infusions I prepped and set up for infusion.